Difference Between Pneumatic And Hydraulic Cylinders
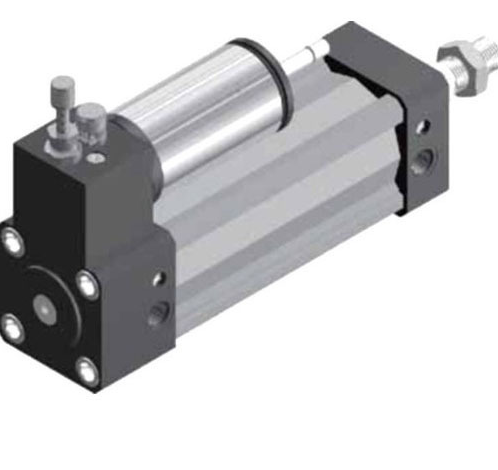
What is a pneumatic cylinder? A pneumatic cylinder is a machine component used to extend and retract a load or push and pull. It’s also known as an air cylinder. The pneumatic cylinder contains compressed air in its body that expands when the piston moves toward it and then contracts when the piston moves away from it. The pressure from this expansion and contraction moves the piston back and forth, like squeezing your hand into a tight fist versus relaxing your fingers, so they’re spread apart.
This post has explained how pneumatic cylinders work, their advantages over hydraulic cylinders, and their disadvantages compared to hydraulics!
Speed
When it comes to speed, pneumatic cylinders are the clear winner. Because they use compressed air as a power source, they can operate at speeds far higher than those of hydraulic cylinders. Their faster operation is especially useful in high-speed applications such as manufacturing machines or assembly lines.
When it comes to low-speed operations like cranes and tractors (think “low” here), hydraulic cylinders prove their worth by providing more torque without having to use more energy than necessary.
Hydraulic Cylinders are also better suited for applications where both sides of the piston must move up or down together—a feature known as “unidirectional.” For example: If you’re lifting something heavy like an engine block with a crane-like device, you’ll want all four wheels on your forklift moving at once so that they don’t slip off each other while trying to lift something heavy off the ground!
Efficiency
A pneumatic cylinder is more efficient than a hydraulic cylinder. Because they do not need to be pressurized, they do not require energy to operate. Hydraulic cylinders must be pressurized by an external source such as a compressor or another cylinder in order to perform work; this requires energy and results in heat loss. Because pneumatic cylinders don’t require external pressure or power sources, they’re much more compact and lightweight than their hydraulic counterparts.
The second major difference between these two types of cylinders is cost: Pneumatic types of cylinders tend to be less expensive than comparable hydraulic ones because they’re simpler machines with fewer moving parts (and no motors).
Space Requirement
Pneumatic types of cylinders are smaller and more compact compared to hydraulic cylinders. This makes them ideal for applications where space is a constraint, such as in the automated assembly line. In addition, a pneumatic cylinder tends to be cheaper than its hydraulic counterparts because it uses compressed air instead of oil as a medium for transmitting power.
Costs
The cost difference between the two types of cylinders is significant. Pneumatic cylinder is less expensive to purchase and maintain, but a hydraulic cylinder generally costs more money upfront. Additionally, a pneumatic cylinder is easier to transport because it can be easily disassembled and moved around in pieces. Hydraulic cylinders are usually only assembled at the job site, meaning that it’s more difficult for workers to get them from one location to another without specialized equipment.
The difference between pneumatic and hydraulic cylinders is that the former uses air to operate while the latter uses liquid. The air pressure in a pneumatic cylinder can be controlled manually or automatically, but it cannot be controlled by an external force such as gravity. Hydraulic cylinders are usually used for heavy lifting because of their superior strength; however, they are more expensive than pneumatic cylinders.